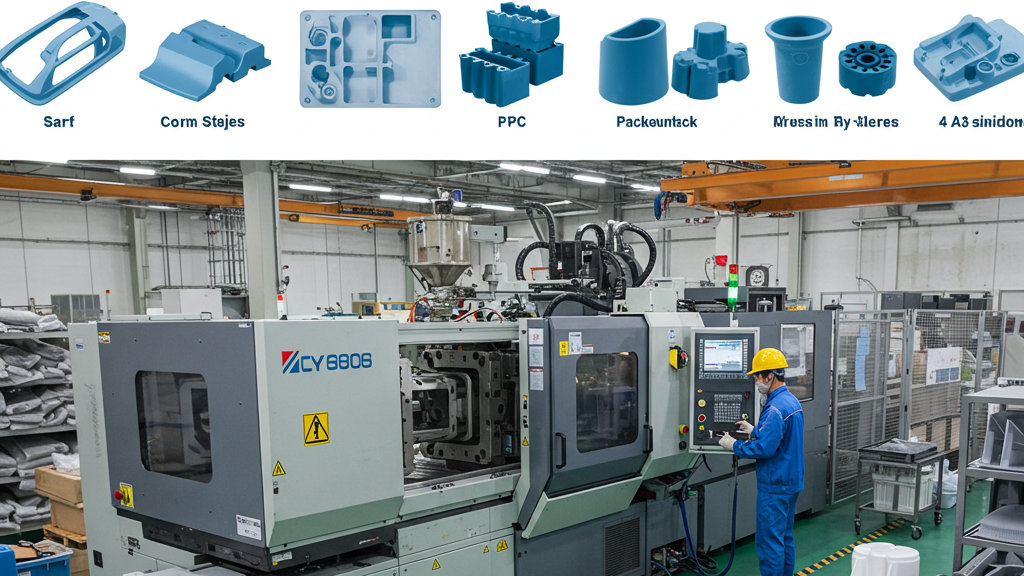
Injection extrusion is a crucial method in plastic processing, enabling the efficient manufacturing of diverse products. However, not all materials are suitable. This article will focus on this aspect, exploring which materials and products can best leverage its advantages.
Once the material suitability is clarified, we need to delve into the process details. Product design, production scale, and cost-effectiveness all influence the final result. Optimizing the process flow is key to achieving efficient production.
Which Plastics Are Suitable for Injection Extrusion?
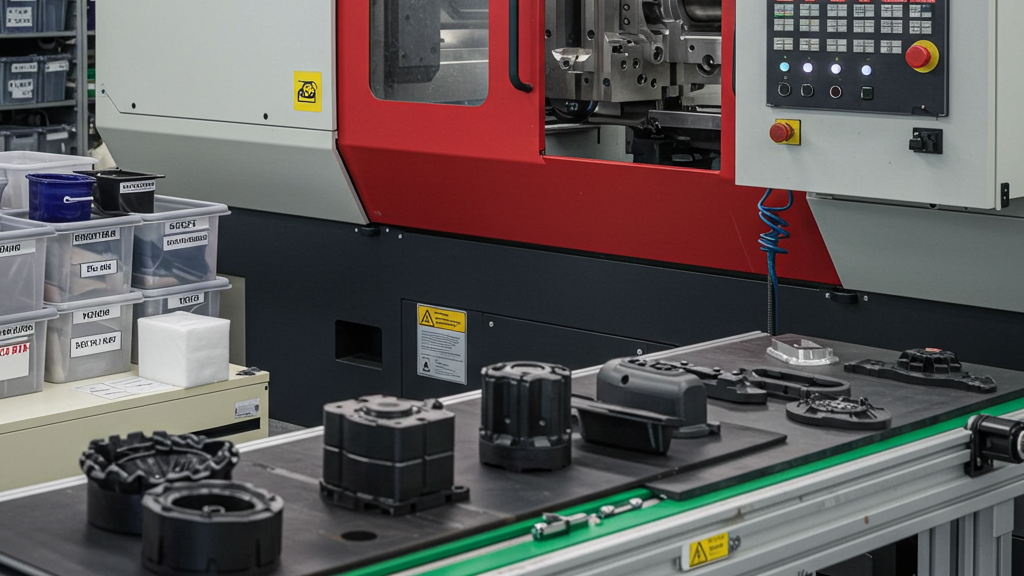
The widespread application of injection extrusion relies on the precise selection of materials. The physical and chemical properties of different plastics determine their performance during the extrusion process.
- Polyethylene (PE): Flexible, chemical resistant, suitable for pipes, films, and packaging.
- Polypropylene (PP): Chemical resistant, heat resistant, impact resistant, suitable for automotive and household appliance parts.
- Polyvinyl Chloride (PVC): Rigid, durable, weather resistant, suitable for pipes, profiles, and cable insulation.
- Acrylonitrile Butadiene Styrene (ABS): Rigid, impact resistant, suitable for electronic product housings, automotive components, and toys.
Which Industries and Products Commonly Use This Process?
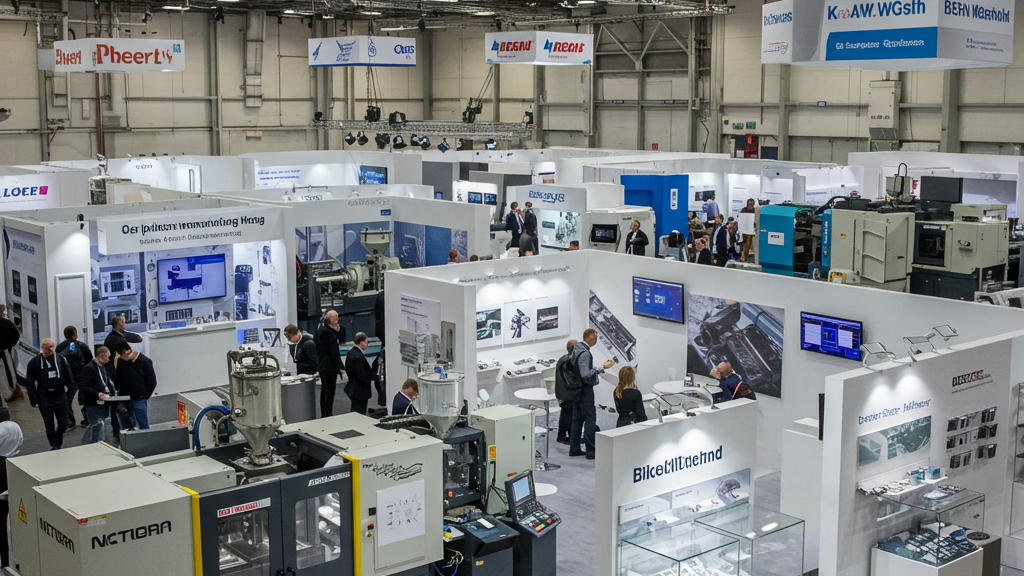
With its efficient and versatile characteristics, injection extrusion plays a significant role in many industries. From everyday plastic products to high-precision industrial components, it’s ubiquitous.
- Automotive Industry: Injection extrusion produces automotive interior and exterior trim components, meeting the demands for lightweighting and aesthetics.
- Construction Industry: Production of weather-resistant and corrosion-resistant plastic pipes, profiles, and door and window materials.
- Packaging Industry: Used for large-scale production of various plastic packaging containers and films.
- Electronics and Electrical Appliance Industry: Manufacturing of electronic product housings and wire and cable insulation layers, ensuring safety and durability.
What Factors Limit the Process Applicability?
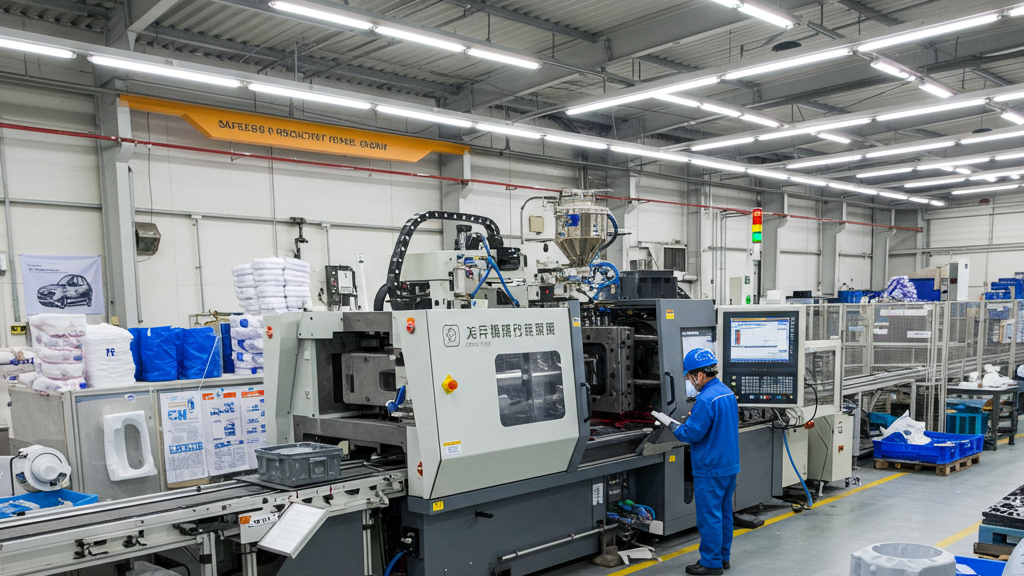
Although injection extrusion is widely used, its applicability is not without limitations. Material, equipment, process parameters, and many other factors jointly determine the quality and production efficiency of the final product. A deep understanding of these key factors is the foundation for optimizing production processes and achieving the best benefits.
- Material Properties: The material’s melt flow, thermal stability, mechanical properties, and shrinkage directly affect product quality.
- Product Design: The product’s geometry, wall thickness, and dimensional accuracy affect mold design and process difficulty.
- Mold Design: The mold’s structure, material, and cooling system affect production efficiency and product quality.
- Process Parameters: Injection pressure, speed, melt temperature, and mold temperature affect the product’s filling effect and surface quality.
Optimization strategy of injection extrusion process
Applicability Factors |
Optimization Strategies |
Notes |
Material Properties | Select suitable resin, control melt flow rate | Consider material viscosity, thermal stability |
Product Design | Optimize structure, reasonable wall thickness, adjust gate position | Avoid stress concentration, sink marks |
Mold Design | Design reasonable runner, cooling, venting systems | Ensure uniform melt filling, effective cooling |
Process Parameters | Control injection pressure, speed, temperature | Adjust parameters for optimal quality |
Improving Process Efficiency and Scope
Optimizing the injection extrusion process to expand its applicability and improve production efficiency is a comprehensive process involving various strategies. By optimizing material selection, product design, mold structure, process parameters, and introducing advanced equipment and automation technologies, significant improvements in production efficiency and product quality can be achieved.
1.Material Optimization: Enhance material performance and applicability by selecting suitable resins and optimizing additives.
2.Product Design Optimization: Improve product quality and production efficiency by improving product structure and gate design.
3.Mold Design Optimization: Ensure uniform melt filling and product quality by optimizing runner, cooling, and venting systems.
4.Process Parameter Optimization: Achieve optimal product quality and production efficiency by precisely controlling injection pressure, speed, and temperature.
Conclusion
The core of optimizing the injection extrusion process lies in comprehensively improving production efficiency and product quality. This requires starting from various aspects such as materials, product design, mold design, and process parameters. By selecting appropriate materials, optimizing product and mold designs, and precisely controlling process parameters, the production process can be significantly improved.
For expert assistance in implementing for your production needs, visit our resource center or contact us. Let’s help you scale up your manufacturing with precision and efficiency!
Post time: Mar-28-2025